К наиболее распространенным рудным соединениям, содержащим железо, относятся: магнитный железняк Fe
04, красный железняк Fe
03, шпатовый железняк ЕеСОз, или углекислое железо (сидерин), железный колчедан — пирит FeS
. Железо входит в состав многих силикатов.
Процентное содержание железа в рудах колеблется от 2 до 26%. В уральских рудах содержится в основном 8—15% железа. Встречаются месторождения с содержанием железа до 50%. Чем больше процент содержания железа в руде, тем процесс получения чугуна облегчается и стоимость полученного железа уменьшается.
В нашей стране залежи железных руд очень велики и вполне обеспечивают развивающуюся гигантскими шагами промышленность. Советский Союз по залежам железа занимает первое место в мире. Наиболее богатые залежи железа находятся на Урале, в Кривом Роге, Карагандинской области, Крыму, районе Курской магнитной аномалии, районах Крайнего Севера и др.
Железо из рудных сосединений добывают методом восстановления. Руду добывают обычно открытым, карьерным или шахтным способом, доставляют на обогатительные фабрики, где подвергают измельчению и обогащению.
Обогащенные руды содержат до 70% железа. Процесс восстановления железа из руд производится в доменных печах углем. При сгорании уголь активно соединяется с кислородом окиси железа и освобождает железо от природы.
Доменные печи вместе с подсобными предприятиями представляют огромные промышленные сооружения.
По характеру работы доменные печи являются печами непрерывного действия. Будучи раз введена в действие, печь функционирует в течение нескольких лет.
Процесс получения железа в доменных печах может быть представлен следующим образом. Через верхнюю воронку доменной печи, которая называется кокошником, механически загружают шихту. Шихтой называется смесь железной руды, кокса и флюсов. Загрузка производится послойно: вначале кокс, затем руда и флюсы. В качестве флюсов используют известняк СаС0
и доломит СаСОз • MgCC>3. Флюсы применяются для понижения температуры плавления образующихся шлаков.
После загрузки доменной печи снизу через так называемые фурмы в домну вдувают подогретый до температуры 600—800° воздух или кислород. За счет горения кокса температура в нижней части печи поддерживается до 1800°, при этой температуре происходит выплавление металла.
По расчетам доменного процесса на каждую тонну выплавленного металла расходуется 2 т руды, 1 т кокса, 0,4 т известняка и 3 т воздуха. На 1 т металла получается 500 кг шлака.
Полученный металл и жидкий шлак периодически выпускают через специальные отверстия.
В процессе выплавки восстановленное железо сплавляется с углем и получается чугун. Чугун содержит углерода от 2,3 до 4,5% и другие примеси: серу, марганец, кремний, фосфор. Для промышленных целей чугун применяется редко вследствие своей хрупкости, недостаточной ковкости. С целью получения из чугуна ковкого железа и стали чугун подвергается дальнейшей обработке.
Процесс переработки чугуна в железо и сталь производится несколькими способами. Один из наиболее старых способов заключается в том, что расплавленный чугун заливают в конвертор (особую печь) и продувают воздухом. За счет кислорода воздуха углерод, содержащийся в чугуне, выгорает, при этом температура расплавленного чугуна повышается до 1700°, из конвертора вырывается пламя с оглушительным грохотом (рис. 72).
Период переработки чугуна этим способом продолжается 15—20 минут. Наиболее совершенным способом выплавки железа и стали является способ регенерации чугуна в мартеновских печах.
Мартеновские печи представляют собой сооружение, состоящее из печи и подогревателей воздуха. Расплавленный чугун загружают в печь и продувают подогретым в подогревателях воздухом.
В последнее время для получения стали из чугуна используют электрические печи. Принцип выплавки стали в электрических печах очень похож на мартеновский процесс.
В полученнной стали содержится от 0,1 до 1,5% углерода. Чем выше процент углерода, тем сталь тверже.
Свойства железа. Железо представляет собой блестящий, серебристо-белый, с синеватым оттенком металл. Химически чистое железо получить очень трудно. Практически в состав чистого железа входит от 0,01% различных примесей и 0,001% углерода.
Удельный вес железа 7,86, температура плавления 1530°, температура кипения 2450°, относительное удли-
Рис. 72. Конвертор для выплавки стали из чугуна. А — частично в разрезе; £ — в действии.
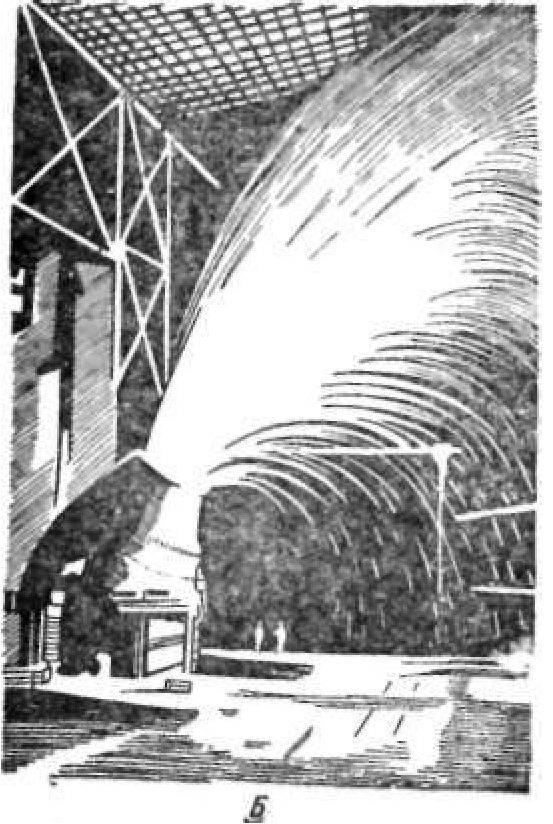
нение 40—50%, твердость по Бринелю 60 кг/мм
, твердость по шкале Мооса 4,5, коэффициент линейного расширения 0,000012.
Железо является неустойчивым металлом по отношению к действиям химических агентов, легко подвергается коррозии. В обычных атмосферных условиях железо ржавеет, покрывается вначале окисловой пленкой, которая постепенно увеличивается. Для предохранения железа от коррозии используют противокоррозийные покрытия цинком, никелем, хромом и различными красками.
В растворах соляной, серной кислоты железо растворяется с выделением водорода.
Железо хорошо плавится с многими металлами. При этом образуются сплавы высокого качества по твердости, ковкости, противокоррозийное™.
Применение железа. Первые сведения об использовании железа относятся к периоду 2000 лет до нашей эры. По архиологическим данным, железо применяли впервые в Египте. В настоящее время железо широко применяется во всех отраслях народного хозяйства, особенно в машиностроении, строительстве.
В зубопротезной технике из сплавов, содержащих железо, изготовляют многие инструменты: окклюдаторы, молоточки, детали вулканизатора, шлифовальных станков и пр. Из стали изготовляют аппараты для штамповки коронок, протягивания гильз, наковальни и др.
Железо является основным металлом для нержавеющей стали, входит в состав хромо-кобальтовых сплавов.
Хром. Хром (Сг) в природе встречается в рудных соединениях, является спутником железа. В промышленных целях для добычи хрома используют хромид, или хромистый железняк Fe (Сг0
Ь- Богатые залежи хромистого железняка распространены на Урале.
Добыча хромистого железняка производится открытым, карьерным или шахтным способом, получение металлического хрома из руды осуществляется методом восстановления при плавке с углем. Процесс восстановления начинается при температуре 1185°.
При плавлении руды хром выплавляется вместе с железом, полученный сплав содержит 4—8% углерода. Высокий процент содержания углерода в сплаве снижает качество сплава, поэтому необходимо снизить процентное содержание углерода. Для удаления углерода применяют метод рафинирования. Сплав плавят в присутствии окиси хрома Сг
0
и закиси железа FeO, при этом выделяющийся углерод из сплава идет на восстановление окиси хрома и закиси железа, в результате снижается процент содержания углерода в сплаве.
Чистый хром_получают методом восстановления окиси хрома алюминием. Этот метод заключается в том, что хромистый железняк сплавляют с содой в присутствии кислорода и получают Na
Cr0
, затем его восстанавливают углем до получения окиси хрома СггОз.
Из окиси хрома чистый хром получают при сжигании порошкообразного алюминия, смешанного с окисью хрома, в специальных огнеупорных тиглях. Реакция восстановления хрома алюминием протекает по уравнению:.
Сг
0
+ 2А1 = 2Сг + Аl
0
Свойства хрома. Хром имеет белый блестящий цвет с синеватым оттенком. Удельный вес его 7,2. Температура плавления 1910°, температура кипения 2200°. Усадка при затвердевании 0,0000081%.
Механические свойства хрома значительно отличаются от свойств других металлов этой группы. Твердость по Бринелю 450 кг/см
, по шкале Мооса 9. Высокая твердость обеспечивает высокую прочность металлу. Удлинение хрома небольшое (6,7%) из-за его большой хрупкости.
Химические качества хрома характеризуются высокой стойкостью к окислению. В обычных атмосферных условиях и в воде хром не окисляется. При нагревании до температуры 1000—1100° в присутствии кислорода воздуха покрывается окисловой пленкой.
В азотной кислоте хром не изменяет свойств, даже царская водка не растворяет его. В растворах серной и соляной кислот хром растворяется медленно, более активно растворяется в крепкой соляной кислоте. В условиях полости рта хром не изменяется.
Высокие химические противокоррозийные свойства позволили применить хром в сплавах для повышения качеств металлов.
Применение хрома. Широкое распространение хром находит в машиностроительной промышленности.
Детали машин, изготовленные из сплавов, в которые входит хром, отличаются высокой прочностью, стойкостью к коррозийным агентам.
Хром используют для покрытия металлических изделий как защиту от коррозии. Процесс покрытия металлов хромом называется хромированием. Хромирование производится электролитическим методом.
В медицинской практике хромирование применяется для покрытия хирургических инструментов, медицинских аппаратов.
Хром является составной частью почти всех видов нержавеющих сталей,.
В зубопротезной технике хром используют для покрытия металлических шин, ортодонтических аппаратов и некоторых металлических зубных протезов, применяемых с лечебной целью, изготовленных из коррозийных металлов.
Увлечение хромированием доходит до того, что в некоторых лабораториях до сих пор хромом покрывают протезы из хромоникелевой нержавеющей стали и даже отдельные коронки.
Практика показала, что в условиях полости рта покрытие хромом металлов, способных коррозироваться, не дает желаемых результатов. В процессе ношения протезов в хромовой оболочке образуются трещины, через которые проникает к металлу слюна и происходит окисление.
Протезы, покрытые хромом, ускоряют стираемость эмали зубов-антагонистов. Хромирование в ортопедической стоматологии допускается при изготовлении временных протезов из медно-алюминиевых сплавов, используемых для лечения переломов челюстей. Хром применяется в виде окиси хрома для приготовления полировочных паст, используемых при полировке деталей машин и металлических протезов.
Никель. Никель (Ni) в природе встречается в виде химических соединений, в чистом виде обнаружен в метеоритах.
Наиболее распространенными рудами, содержащими никель, являются: мышьяково-никелевый блеск NiAsS, гарньерит NiMg-H
Si0
Залежи никелевых минералов, имеющие промышленное значение, встречаются в Карельской АССР, Оренбургской области, Красноярском крае, на Урале.
Для получения никеля из руды применяют несколько способов. Наиболее распространенным является способ агломерации шихты.
Руду сплавляют в шахтной печи с гипсом и известняком, полученный сплав в жидком виде загружают в конвертор, в котором он продувается воздухом для окисления и шлакования железа. В результате окисления получается сульфид никеля NiS с небольшим содержанием вяем чистого никеля. При дальнейшем обжиге сплава никель освобождают от серы, образующийся сернистый газ SO2 улетучивается, никель переходит в закись никеля NiSC>4. Чистую закись никеля направляют на электроплавку в смеси с древесным углем и получают чистый никель. Для получения химически чистого никеля применяют электролитический способ, когда никель получают из раствора сернокислого никеля, i.
Свойства никеля. Никель — металл серебристо-белого цвета. Удельный вес его 8,9. Температура плавления 1455°, температура кипения 2900°, скрытая теплота плавления 73, теплопроводность 14, усадка 0,000013. Никель обладает магнитными свойствами,.
По механическим свойствам никель близок к железу.
Твердость по Бринелю 68—78 кг/мм
, удлинение 35%, временное сопротивление 50 кг/мм
, твердость по шкале Мооса 5, обладает хорошей ковкостью.
Химические свойства никеля приравниваются к свойствам благородных металлов. На воздухе и во влажной среде никель не окисляется.
Концентрированные кислоты (серная и соляная) действуют на никель слабо. В азотной кислоте и ее растворе никель растворяется.
При нагревании до температуры свыше 500° никель окисляется, покрывается окисловой пленкой.
Применение никеля. В связи с высокими противокоррозийными свойствами в обычных условиях, прочностью никель с давних времен используют для покрытия коррозийных металлов. Тонкая пленка никеля хорошо защищает от окисления.
Процесс никелирования широко используется в промышленности для покрытия деталей машин. В автомобильной промышленности никелем покрывают не защищенные от коррозии детали корпуса машин. Покрытие поверхности металлов никелем производится электролитическим путем.
В медицинской практике никелем покрывают хирургические инструменты, аппараты.
Никель входит в состав многих сплавов и придает сплаву новые свойства, повышающие химическую устойчивость.
Сплав никеля с хромом называется нихромом. Нихром употребляется для изготовления проволочных спиралей электронагревательных приборов.
Различные сорта нержавеющей стали содержат от 10 до 30% никеля, эти сорта стали обладают высокими противокоррозийными свойствами и хорошими механическими качествами.
Нержавеющая сталь, используемая для зубных протезов, содержит от 8 до 24% никеля и обладает многими положительными качествами.
Никель, введенный в состав золотого сплава (от 5 до 10%), вполне заменяет платину. Новый сплав получается вязким, обладает высокой крепкостью.
Паяние никеля производится золотом, серебряным и стальным припоем, отбеливание — растворами кислот соляной и азотной (см. «Нержавеющая сталь»).
Кобальт. Кобальт (Со) в природе встречается в рудных соединениях. Наибольшее промышленное значение имеют мышьяковисто-кобальтовые руды и сернистые кобальтсодержащие руды железа, никеля и меди.
Из числа мышьяковисто-кобальтовых руд чаще встречается скуттерудит с содержанием кобальта от 10 до 20%, кобальтин с содержанием 29—34%.
Из сернисто-кобальтовых руд с высоким процентом содержания кобальта встречается карролит C11C02S4 (27—42%). Чаще руды этой группы содержат кобальт в виде примесей, а в основном руда состоит из железа, никеля и меди.
Добыча кобальта из кобальтсодержащих руд представляет собой сложный технологический процесс и связана с трудностями отделения металлов, входящих в состав руды.
Обогащенную руду подвергают обжигу и плавке. После отделения основного металла шлаки, содержащие кобальт, обрабатывают подкисленной НС1 водой, из полученного раствора отделяют химическим путем гидроокись кобальта Со (ОН)
. Последнюю переводят методом прокаливания в окись кобальта, которую восстанавливают углем до получения чистого металла.
Свойства кобальта. Металл белого цвета с красноватым оттенком, удельный вес 8,7—8,9, температура плавления 1490°, температура кипения 3185°. Твердость по Бринелю 124 кг/мм
. Несмотря на высокую твердость, обладает хорошей ковкостью и тягучестью. Прочность на разрыв 26 кг/мм
. Обладает малой усадкой при плавлении.
При обычных условиях на воздухе не окисляется, при нагревании до температуры 300° покрывается окисловой пленкей. В растворах кислот соляной, азотной и серной медленно растворяется.
Применение кобальта. В чистом виде металл почти не применяется, входит в состав сплавов. Сплавы, содержащие кобальт, называются сверхтвердыми сплавами (стеллит, победит и др.).
Сверхтвердые сплавы в основном применяются в металлообрабатывающей промышленности для изготовления сверл, резцов.
Сплавы кобальта обладают высокими
магнитными свойствами и применяются для выработки постоянных магнитов.
В ортопедической стоматологии кобальт начал применяться сравнительно недавно (с 1933 г.) в виде хромокобальтовых сплавов под названием виталлиума. В состав сплавов, выпускаемых отечественной промышленностью, входят следующие элементы.
1.
Хрома 30—32%, кобальта 62—63%, никеля следы, молибдена 5,1—5,5%, железа 0,7%, марганца 0,5%, кремния 0,3%, углерода 0,4%.
2.
Хрома 25—28%, кобальта 62—64%, молибдена 5%, железа 2,5—3,5%, кремния 0,3—0,5%, марганца 0,5-0,7%.
Хромокобальтовые сплавы обладают многими положительными качествами, необходимыми для металлов, применяемых в ортопедической стоматологии. Температура плавления 1400°, удельный вес 8,3, твердость по Бринелю 370 кг/мм
, удлинение 10%, сопротивление разрыву 89,6 кг/мм
, усадка при отливке 1,8—2%.
Хромокобальтовые сплавы имеют высокие противокоррозийные свойства, при отливке деталей протезов сплав обладает хорошей текучестью, дает малую усадку, хорошо куется и штампуется. Для плавления хромокобальтовых сплавов применяют высокочастотные плавильные установки. Хромокобальтовые сплавы паяются припоем Цитрина и золотым припоем 750-й пробы.