28. Способ стерилизации стенса (объяснение в тексте).
27. Устройство для постоянного разогрева стенса (объяснение в тексте).
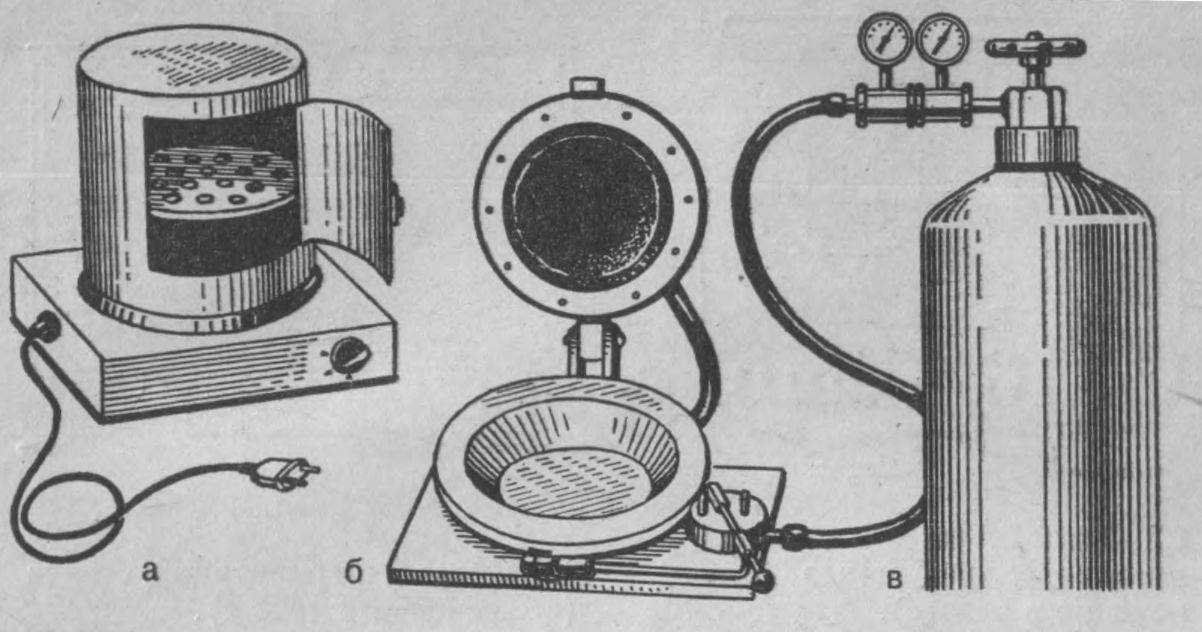
29. Рабочие узлы стоматологической ортопедической пресс-установки, а — термокамера, б — пресс-форма, в — узел, обеспечивающий давление.
обозначены границы ложки, изолированы фольгой или лейкопластырем уплотненные участки, закрыты (гипсом или цементом) места поднутрений.
На зубы следует нанести 2—3 слоя лейкопластыря с целью создания места для эластической слепочной массы и т. д.
При изготовлении ложек с использованием литьевого прессования целесообразно применять четырехместные шприц-кюветы. Для формовки можно использовать карбс?5ласт. В порошок карбопласта мы добавляем, если имеются, остатки порошков других акриловых пластмасс (норакрил, этакрил и т. п.). В жидкость добавляем остатки мономера от других видов пластмасс.
При загипсовке моделей с восковым шаблоном в четырехместную кювету устанавливали один центральный литник диаметром 5 мм и от него разводящие — диаметром 5,5 мм. Выводные каналы не создаем. Пластмассу вводим в жидкотекучем состоянии в неохлажденную кювету. Уплотнение заформованной массы не проводим.
При изготовлении ложек путем обжима листового термопластического материала следует использовать пневмоформовочный аппарат ППС-1, созданный в Центральном НИИ стоматологии МЗ СССР. Мы на протяжении 10 лет для этой цели используем стоматологическую ортопедическую.
пресс-установку (СОПУ) конструкции
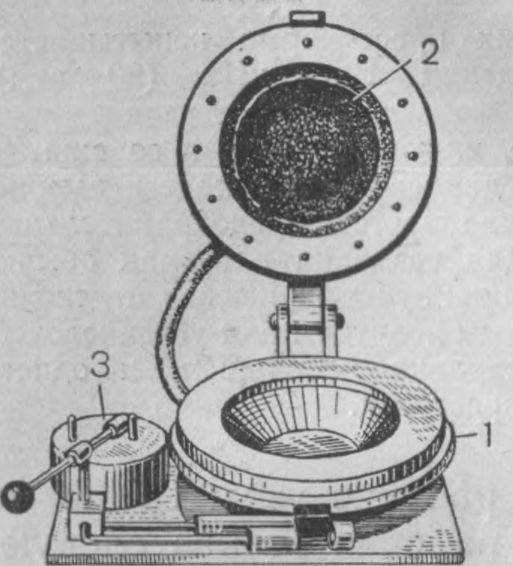
30. Пресс-форма. Общий вид. 1—основание, 2—резиновая диафрагма, 3 — клапанная система.
31. Схематическое устройство прессформы.
— основание, 2 — крышка, 3 — резиновая диафрагма, 4 — замыкающее кольцо, 5 — ручка-защелка, 6 — шарнир, 7 — модель, 8 — пластинка термопластического материала, 9 — клапанная система.
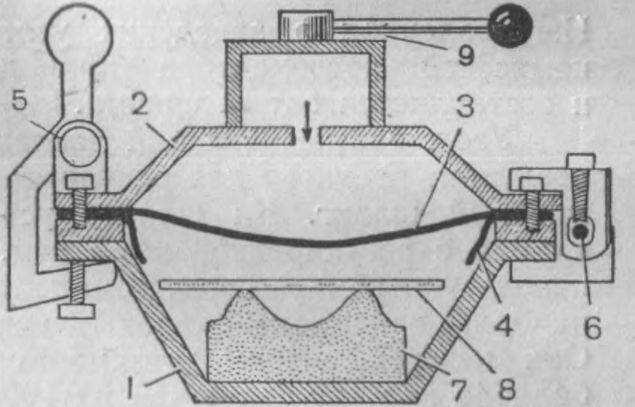
Э. Я. Вареса СОПУ состоит из трех рабочих узлов: термокамеры, пресс-формы и узла, обеспечивающего давление (рис. 29).
Термокамера. В простейшем виде представляет бытовую электрическую плитку с закрытой спиралью и терморегулятором, на который установлен металлический (из 1 мм жести) цилиндр высотой 100 мм и диаметром чуть больше нагревательного диска электроплитки. В крышке термокамеры имеется гнездо для термометра. Внутри на расстоянии 50 мм от плитки укреплена крупнопетлистая сетка, на которую помещается для разогревания термопластический материал. Сбоку имеется дверца.
Пресс-форма (рис. 30). Основу пресс-формы составляют основание линзообразной формы и плоская крышка из 5 мм железа (CT-3) Основание приварено к опорной плите, что обеспечивает прочность и устойчивость на рабочем столе. Крышка и основание соединены шарниром. В момент прессования крышка удерживается у основания шарниром и ручкой-защелкой (рис. 31). К основанию крышки прижимным кольцом с помощью болтов (М6Х15) укрепляются резиновая диафрагма и замыкающее резиновое кольцо толщиной 2—2,5 мм, вырезанное из автокамеры. Через отверстия на крышке поступает сжатый воздух и оказывает давление на резиновую диафрагму. Подача воздуха осуществляется при помощи пневматического крана Б-71-22, который располагается на основании прессформы. Ручка крана сконструирована таким образом, что подача воздуха может быть произведена только в положении, когда пресс-форма закрыта. Это достигается наличием предохранительной пружины в замке пресс-формы. В зависимости от проводимой операции возможна медленная или быстрая подача сжатого воздуха. В крышке пресс-формы вварен предохранительный выпускной клапан.
Изготовленная в заводских условиях пресс-форма испытывается комиссией котлонадзора при давлении 1960 кПа (20 атм), и составляется акт ее приема.
Узел, обеспечивающий давление, включает: баллон со сжатым воздухом, редуктор для регулировки давления на выходе и высокопрочный шланг. На шланге устанавливается предохранительный клапан с регулировкой на 9 атм. Для создания давления обычно используют компрессоры. Для небольших зуботехнических отделений наиболее приемлемы баллоны со сжатым воздухом или углекислотой. Они невзрывоопасны, стоимость заправки небольшая, и одного баллона хватает более чем на 1000 прессовок.
Как следует из описания, рабочие узлы СОПУ не сложны. Последовательность рабочих этапов следующая: 1) включить электроплитку термокамеры в сеть, и установить с помощью регулятора температуру, необходимую для размягчения используемого термопластического материала, 2) открыть вентиль баллона с углекислотой; 3) с помощью регулятора редуктора создать рабочее давление, не превышающее 8 атм `; 4) открыть пресс-форму и на основании ее установить гипсовую модель; 5) в термокамеру поместить пластинку термопластического материала; 6) как только термопластический материал размягчится, его из термокамеры пинцетом перенести на модель, закрыть крышку и открыть клапан. Углекислый газ поступает между крышкой и диафрагмой, давит на диафрагму и она, натягиваясь, обжимает пластинку материала по модели (см. рис. 31).
Чтобы произошло охлаждение отштампованной пластинки, выжидают, в зависимости от теплоемкости материала, 1—3 мин, сжатый воздух или углекислый газ выпускают из камеры путем смещения рукоятки клапана системы в обратную сторону. Камеру открывают и модель с отжатой по ее поверхности пластинкой извлекают. С помощью зубного сепарационного или специального диска излишки обрезают, отступая кнаружи на 1 мм от заранее определенных границ.
Пока в пресс-форме происходит охлаждение отпрессованной термопластической пластинки, следующая пластинка нагревается. Таким образом, рабочий цикл при прессовании перекрывается и при большом числе прессовок составляет не более 3 мин. Соответственно возрастает и производительность труда. Например, при изготовлении жесткой индивидуальной ложки производительность труда зубных техников на данном этапе возрастает более чем в 20 раз по сравнению с технологией изготовления индивидуальной ложки путем замены воска пластмассой.
Положительные стороны СОПУ по сравнению с аппаратом ППС-1: невысокая стоимость при серийном выпуске; отсутствие сложных узлов, приборов, схем, а поэтому и простота работы, ремонта и замены деталей; более высокая производительность труда; меньше (примерно на 30 %) расход термопластического материала; возможность использования для штамповки жесткого (типа оргстекла) и эластического (типа полиэтилена) термопластического материала толщиной от 0,2 до 5 мм с температурой размягчения до +250 °С; более точное изготовление деталей протезов; возможность проведения большего числа производственных операций.
Помимо изготовления индивидуальных ложек, с помощью СОПУ можно просто и быстро изготовить: защитные колпачки после препаровки зубов; защитные каппы после препаровки зубов; каппы для фиксации лечебных повязок; временные шинирующие капповые аппараты с покрытием жевательной поверхности зубов; временные шинирующие аппараты без покрытия жевательной поверхности зубов; постоянные шинирующие аппараты; базисы частичных пластиночных протезов; базисы частичных пластиночных протезов с пластмассовыми дентоальвеолярными кламмерами; базисы частичных съемных пластиночных протезов с пластмассовыми многозвеньевыми кламмерами; базисы дуговых протезов; базисы полных съемных протезов; базисы сложных челюстно-лицевых и послерезекционных протезов; обтураторы; защитные небные пластинки после уранопластики; базисы съемных ортодонтических аппаратов без разобщения прикуса; базисы ортодонтических аппаратов с разобщением прикуса; базисы ортодонтических аппаратов, фиксирующихся с помощью капп; основание каппы типа Бынина и Шварца; детали к аппаратам Френкеля, Брюкля, Андерсена и др.; глазные протезы; подборочные пращи, пластмассовые коронки; заготовки для отливки дуговых протезов, для литых коронок и цельнолитых мостовидных протезов и многие другие виды протезов или их заготовки.
С помощью пресс-формы можно вводить под давлением базисную пластмассу через литниковые отверстия методом литьевого прессования в кювету после вытравления воска и обеспечить полимеризацию быстротвердеющей пластмассы под непрерывным давлением до 8 атм.
Наиболее подходящим материалом для изготовления индивидуальных ложек являются пластинки оргстекла (ПММА) толщиной до 2 мм. На промышленных предприятиях обычно имеются отходы, и по договоренности их можно приобрести.
Пластинки ПММА удобны тем, что при нагревании они не «сбегаются», не сокращаются, и их можно разогревать в свободном состоянии. Большинство других листовых термопластов при нагревании сокращаются. Поэтому их перед помещением в термокамеру надо зажимать в специальные металлические кольца.
Индивидуальные ложки, отштампованные из листового термопластического материала, имеют гладкую поверхность, вследствие чего эластические слепочные массы на них плохо удерживаются.
Для создания ретенционной поверхности на индивидуальной ложке на модель помещают полиэтиленовую пленку и сверху слой марли, пропитанный канифольным клеем. В процессе штамповки марля соединяется с пластинкой ПММА, создавая, таким образом, ретенционную поверхность. Можно на модели создавать отверстия или помещать полоски лейкопластыря липкой стороной кнаружи. Во время штамповки полоски прочно соединяются с пластинкой.
Укрепление прикусных валиков. На изготовленные индивидуальные ложки следует сразу же укреплять стандартные прикусные валики. Валики, о чем уже было сказано следует изготавливать из отходов воска или стенса, путем выдавливания через профильные отверстия с помощью пресса.
Определение центральной окклюзии и получение функциональных слепков. Индивидуальные ложки с прикусными валиками врач припасовывает в полости рта, используя пробы Гербса. Затем создает протетическую плоскость и определяет центральную окклюзию «под прикусом» по рекомендуемой в последнее время методике Н. В. Калининой (1979) или же по методике, рекомендуемой А. Л. Сапожниковым (1983).
Получение моделей по функциональным слепкам. По функциональным слепкам зубной техник должен получить двуслойные гипсовые модели, с упрочненной поверхностью, обращенной к протезному ложу, используя ранее изложенные технологические положения. Отлитые, но невскрытые модели благодаря «отметкам» на прикусных валиках оставляют в положении центральной окклюзии и загипсовывают в окклюдатор (или в артикулятор) и только после этого вскрывают.