Для точного переноса на огнеупорную модель мест расположения плеч кламмеров по нижнему краю каждого плеча создают ступеньку из тугоплавкого бюгельного воска.
Для создания разобщения между дугой протеза и слизистой оболочкой в местах ее расположения устанавливают изоляцию из свинцовой пластинки, бюгельного воска или лейкопластыря. Она должна иметь равномерную толщину, плотно прилегать к модели и иметь гладкую наружную поверхность. Толщина прокладки в области расположения сетки—1,5—2 мм, под дугой — 0,5—0,8 мм, что зависит от степени податливости слизистой оболочки тканей протезного ложа и подвижности опорных зубов.
Подготовленную таким образом модель опускают на не сколько минут в холодную воду для удаления воздуха из пор и укрепляют на резиновом основании кюветы строго по центру с помощью мольдина или пластилина (рис. 62). Накрыв крышкой основание кюветы, в одно из трех отверстий наливают дублирующую гидроколлоидную массу (агар-агара — 3— 3,5 %, этиленгликоля — 57—60 %, дистиллированной воды — 28—30 %, триэтаноламина 10—12%), нарезанную мелкими кусочками, помещают в эмалированный или фарфоровый сосуд с крышкой и ставят в водяную баню для расплавления при температуре + 80 °С в течение 1 ч. Охладив до +424- +68 °С, массу наливают в одно из отверстий кюветы до появления ее из других отверстий и ждут полного затвердевания, затем помещают в холодную воду. Удалив дно кюветы, подрезают массу вокруг основания модели и осторожно выталкивают модель.
В центре формы устанавливают полый металлический конус и отливают модель из огнеупорной массы.
Для получения огнеупорных моделей используют различ ные формовочные массы, основным требованием к которым является оптимальное расширение модели при нагревании, позволяющее компенсировать усадку сплава.
Огнеупорная модель должна выдерживать температуру до 1400+1600 °С и при этом не деформироваться. Выпускаемые в СССР огнеупорные массы «Силамин», «Кристосил» и «Бюгелит» имеют различный состав и соответственно различные термические коэффициенты объемного расширения.
«Силамин» представляет собой огнеупорную смесь тонкого помола, имеющую в своем составе фосфатные связки; термический коэффициент объемного расширения— 1,8% при 800 °С. Материал химически устойчив, гигроскопичен, огнеустойчив (1700 °С), растворяется в водопроводнойводеснача лом схватывания 7—10 мнн и окончанием — 50—60 мин Для изготовления одной модели берут 100—120 г порошка, перед этим тщательно перемешанного в банке, высыпают в чистую сухую резиновую чашку и вливают воду в количестве указанном в инструкции Для более точного определения количества порошка умножают массу сухой модели на 1,7 Энергичным перемешиванием порошка в воде получают зыбкую, однородную, текучую массу, которой на вибраци онном столе малыми порциями заполняют форму в течение 3—5 мин
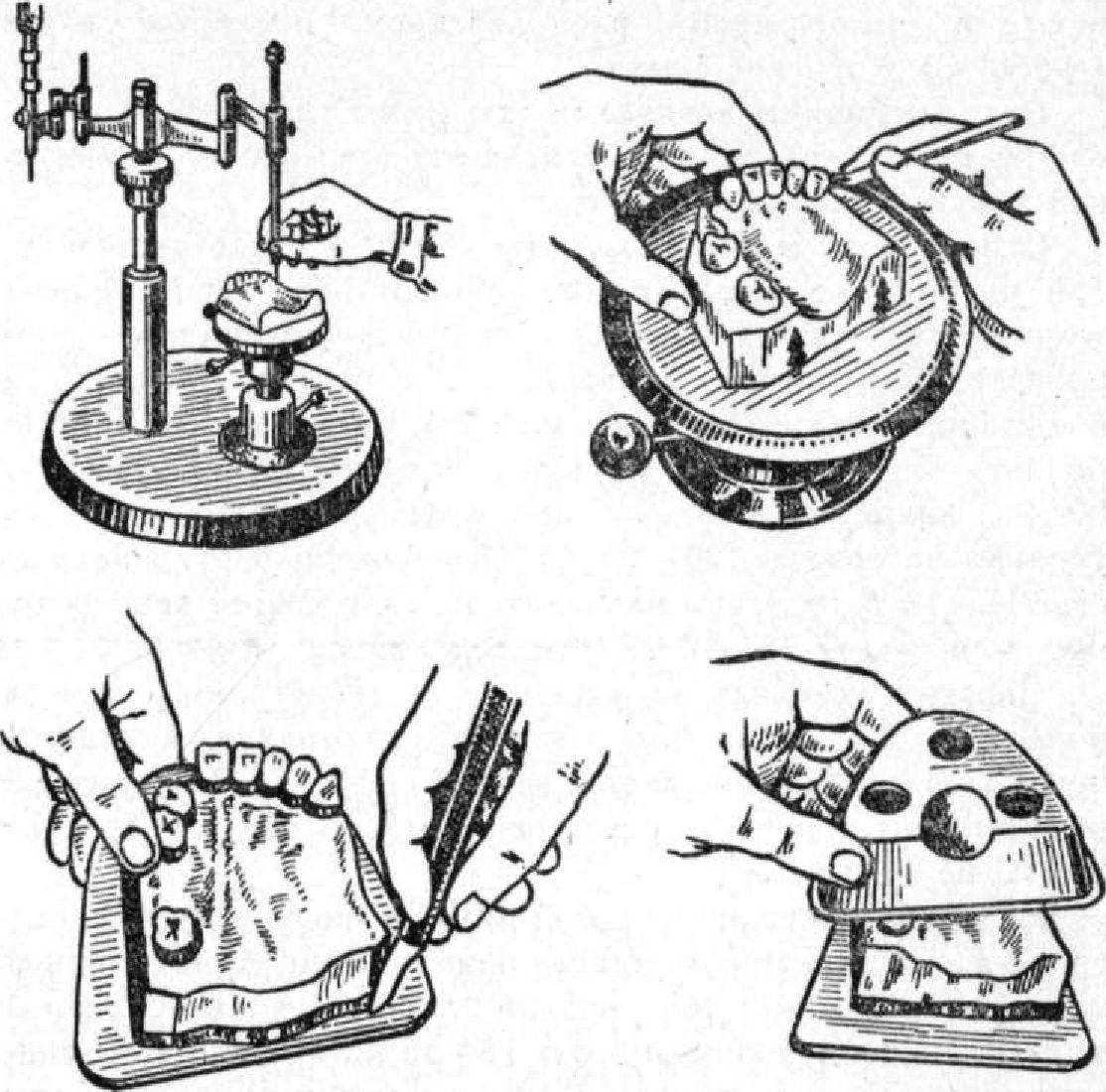
62. Подготовка модели к дублированию (В Ю. Курляндский).
Для уплотнения модели и увеличения ее расширения при нагревании, компенсирующего усадку сплава, затвердевать масса должна в условиях вакуума, что способствует отсасыванию воздуха из массы. После исчезновения с поверхности модели влажного блеска удаляют воронку и оставляют форму до полного затвердевания массы еще на 45 мин.
Высвобождение огнеупорной модели из формы следует производить с большой осторожностью путем разрезания дублирующей массы. Модель сушат на воздухе (15—20 мин), в сушильном шкафу при температуре +180 200 °С (30 мин) и для заполнения пустот, образующихся в ней после удаления влаги, подвергают химической обработке и пропитке. Для этого модель погружают в 2 % раствор хлористоводородной кислоты (940 мл воды и 60 мл кислоты), имеющей температуру + 40 + -+45 °С, доводят ее до +97 "С в течение 20—30 мин и выдерживают при этой температуре 20—30 мин Затем модель промывают в горячей воде, высушивают в сушильном шкафу прн температуре +150 °С в течение 30 мин и пропитывагат в закрепителе — расплавленном пчелином воске (-|-150
С) в течение t мин.
Охлажденная на воздухе модель имеет гладкую, твердую, слегка липкую поверхность, пригодную для моделирования на ней каркаса бюгельного протеза.
Огнеупорная масса «Бюгелит» — «ОЛ» представляет собой чистый кварцевый песок, обработанный при высоких температурах (кристобаллит) и связующее вещество — гидролизованный раствор этилсиликата с отвердителем (10% водный раствор гидрата окиси натрия). Состав массы: кристобаллит — песок (30 — 40 %), кристобаллит пылевидный (30— 50%), кварц пылевидный или другие пылевидные огнеупорные материалы (20—40 %). Отверднтель берут в количестве 17—18 % от массы наполнителя. Связующим веществом является пексон (5—10% от массы наполннтеля).
Порошок устойчив на воздухе и не теряет своих свойств в течение года. После замеса массы схватывание начинается через 3—5 мин и оканчивается через 40—50 мин. Термический коэффициент линейного расширения массы при температуре 900 °С не менее 1,4 %.
После извлечения гипсовой модели полученную форму сразу же заполняют заранее приготовленной огнеупорной массой во избежание образования неточностей в огнеупорной модели. На 100 г порошка берут 18—25 мл отвердителя (гидролизованный этилсиликат). Массу готовят на вибростоле при постоянном перемешивании (лучше в условиях вакуума) и, расположив форму рядом с чашкой, заполняют ее малыми порциями. После выдерживания на вибраторе в течение 2— 3 мин и сглаживания поверхности последнюю посыпают песком. Через 30 мин модель осторожно освобождают путем надрезания дублирующей массы, сушат на воздухе и в сушильном шкафу при температуре от +40 °С до -(-200 °С и после извлечения из шкафа в горячем виде покрывают всю поверхность тонким слоем гидролизованного этилсиликата (кроме дна). После высыхания покрытия эту операцию повторяют еще два раза.
Пропитку модели производят в расплавленном (-f 150 °С) парафине или воске.
Огнеупорная масса «Крнстоснл-2» состоит из огнеупорного порошка — кристобаллнта, имеющего в своем составе фосфатные связки.
Порошок гигроскопичен, растворяется в воде, начало схватывания наступает через 5—7 мин, отвердевание — через 40 мнн, термический коэффициент объемного расширения при температуре 900 "С—1,4 %.
Связующей жидкостью служит гидролизованный тетраэтилсиликат, который можно приготовить путем смешивания 55 мл этнлснликата с 36 мл чистого этилового спирта и 16 мл I % раствора хлористоводородной кислоты. После 5-минутного взбалтывания раствор готов к употреблению.
Для приготовления массы берут 100 г порошка и добавляют 25 мл гидролизованного тетраэтилсиликата, тщательно перемешивают и заполняют форму на вибростоле (лучше под вакуумом) в течение 10 мин. Окончательное затвердевание модели наступает через 30—40 мин.
Перед моделированием из воска конструкции каркаса бюгельного протеза необходимо перенести с гипсовой на огнеупорную модель чертеж всех его элементов. Точному воспроизведению положения плеч кламмеров помогают ступеньки на поверхности опорных зубов, соответствующие ограничительным линиям на гипсовой модели. Образованию зазора между дугой и слизистой оболочкой протезного ложа способствуют прокладки, уложенные на гипсовой модели в соответствующих местах и воспроизведенные на огнеупорной модели.
Перед наложением на огнеупорную модель восковых деталей каркаса бюгельного протеза, изготовленных по специальным силиконовым матрицам «Формодент» или индивидуально, модель покрывают одним слоем тонкого бюгельного воска, хорошо нагретого и позволяющего плотно обжать всю поверхность модели. Этим самым достигаются более плотное прилегание восковой композиции к поверхности модели, большая прочность ее и минимальная усадка воска.
Для моделирования кламмеров используют восковые нити толщиной 0,8—1 мм или заготовки матрицы, которые укладывают на восковое основание опорного зуба согласно отмеченным границам и прикрепляют к базисной пластинке упругим моделировочным воском.
Часть кламмера, расположенная на опорной части зуба, должна быть толще и иметь в профиле полукруглое сечение, в ретенционной части зуба — тоньше и круглое сечение. Затем моделируют тело кламмера с окклюзионной накладкой и отростком, направленным к дуге.
Дугу верхнего протеза моделируют из восковой полоски полуовального сечения шириной 4—5 мм с последующим ее расширением до 6— 8 мм за счет приплавления упругого моделировочного воска к восковой базисной пластинке.
Седловидные части каркаса бюгельного протеза должны иметь приспособления в виде петель или решетки для надежной фиксации в пластмассовом базисе.
Для обеспечения свободного поступления расплавленного металла в выплавляемые формы необходимо правильно изготовить литниково-питающую систему.
Заполнив воском отверстие литниковой чаши в основании модели {диаметр 6—8 мм), приступают к изготовлению и установке моделей литников, которые соединяют главный восковой стояк с более толстыми частями воскового каркаса протеза. Это обеспечивает хороший доступ расплавленного металла к тонким частям конструкции каркаса.
Количество литников, форма и толщина зависят от сечения отливаемых деталей, их расстояния от основного стояка, способа плавки и заливки металла.
Форма литников — прямоугольная или цилиндрическая, толщина — в 3—4 раза больше восковой заготовки. Это необходимо для получения гомогенной структуры сплава отлитой детали и предупреждения образования усадочных раковин. Для этого же на моделях литников ближе к отливке моделируют из воска шаровидное утолщение, улавливающее шлаки и повышающее чистоту поверхности. При коротких литниках утолщения не моделируют.
`.
Различают крестовидную, крыльчатую и одноканальную литниковые системы.
Крестовидную систему применяют при отливке через отверстие (главный канал) в огнеупорной модели сложных конструкций дуговых протезов. При этом одним концом литник прикрепляют к месту соединения дуги с сеткой, другим — к восковому стояку. Остальные литники соединяют середину дуги, многозвеньевые кламмеры, места соединения отростка кламмера с дугой и др.
Крыльчатая система образована дугообразно изогнутыми круглыми литниками диаметром 3—4 мм, соединяющими восковой стояк с элементами каркаса дугового протеза. Изгиб литников устраняет резкое изменение направления расплавленного металла и уменьшает напряжение в сплаве при его охлаждении.
Однокаиалыная система образована литником толщиной 5—6 мм, который устанавливают у основания литниковой чаши по направлению вращения модели при отливке. Постепенно истончаясь, литник прикрепляется к каркасу дугового протеза.
Одноканальную систему можно применять при отливке сложных конфигураций или металлического базиса с использованием центробежного или вакуумного литья.
После окончательного моделирования воскового каркаса дугового протеза, установки литниково-питающен системы и перед окончательной формовкой блока огнеупорной модели производят следующую подготовку. При изготовлении огнеупорной модели с использованием масс на основе фосфатных связок («Силамин», «Крнстоснл») восковую композицию каркаса обрабатывают растительным маслом (эвкалиптовым) для заглаживания поверхности воска и устранения насечек и трещин. После протирания маслом поверхности воска сразу же обмывают этот участок ацетоном или эфиром, которые растворяют избыток масла и закрепляют гладкую поверхность. Затем восковую конструкцию моют холодным раствором мыльного порошка («Новость») и, удалив воздухом образовавшиеся мыльные пузыри, приступают к обмазке. Подготовку восковой композиции на огнеупорной модели при этилсиликатной связке («Бюгелит») производят с помощью ацетона и жидкого раствора тонкодисперсной массы «Бюгелит» с этилснликатом.
Отмоделированный на огнеупорной модели восковый каркас бюгельного протеза с литниково-питающей системой покрывают огнеупорной оболочкой и формуют в кювету-опоку.
Огнеупорная оболочка должна выдерживать температуру расплавленного металла (1700
С), иметь одинаковый термический коэффициент объемного расширения с материалом, из которого изготовлена огнеупорная модель, точно передавать рельеф отливаемой детали, быть газопроницаемой и легко отделяться от отливки.
Лучшим материалом для огнеупорной оболочки служит тот, из которого изготовлена рабочая модель, па которой будет производиться отливка.
При отливке каркаса бюгельного протеза на модели из силамина для создания огнеупорной оболочки используют ту же массу. Ее приготовляют небольшими порциями (10— 15 г) и, установив модель на вибростол, кисточкой наносят на все восковые детали. После высушивания укрепляют модель на подставке с помощью пластилина, накрывают картонным кольцом, верхний край которого должен быть выше края модели на 10—15 мм, и заполняют его огнеупорной массой («Силамин»), замешанной на воде в соотношении 5,5:1.
После затвердевания массы картон удаляют, накрывают металлическим кольцом, обложенным изнутри асбестом, и формуют кварцевым песком с двумя влажными пробками (50 % раствор жидкого стекла), в которых создают отверстия для выхода газа.
Для создания огнеупорной оболочки можно использовать маршалит, смешанный с гидролизованным тетраэтилсиликатом.
Маршалит — кварцевая мука, мелкозернистый порошок с содержанием не менее 98 % двуокиси кремния, тщательно промытый, освобожденный от примесей н прокаленный при температуре 900 °С в течение 2 ч.
Этилсиликат — этиловый эфир ортокремниевой кислоты, содержит 30—34 % двуокиси кремния и 0,15 % хлористоводородной кислоты. Применяется как связывающее вещество для маршал ита.
Для увеличения связывающих свойств его подвергают гидролизу. Для этого берут 75 мл этилсиликата, добавляют 105 мл этилового спирта и 45 мл дистиллированной воды, подкисленной 0,2—0,3 % раствором хлористоводородной кислоты (на 0,5 л воды — 1 — 1,5 мл кислоты, имеющей относительную плотность 1,19). После постоянного взбалтывания по достижении в растворе температуры +45 "С добавляют еще 75 мл исходного этилсиликата и, продолжая взбалтывать, ждут понижения температуры и исчезновения мути. Охлажденный водой раствор оставляют на сутки для приготовления обмазки. Последнюю получают путем смешивания 3 частей раствора этилсиликата с 1 частью маршалита при непрерывном помешивании, добиваясь смеси сметанообразной` консистенции.
Смесь на восковые детали наносят путем погружения всей восковой конструкции в сосуд или поливкой восковых деталей этой смесью в несколько приемов с последующим нанесением кварцевого песка. Это предупреждает стекание облицовочной смеси с восковых моделей, увеличивая толщину и прочность огнеупорной оболочки.
После высушивания в парах аммиака и проветривания на воздухе приступают к формовке восковой модели. Для этого подбирают кювету соответствующего размера и накрывают ею облицованную модель, установленную на подопочный конус.
Кювету с подопочным конусом и моделью устанавливают на вибростол и заполняют формовочной массой, в качестве которой используют кварцевый песок и гипс в соотношении 1:1, с двумя влажными пробками.
Для улучшения качества отливок, экономии металла и формовочных масс, снижения трудоемкости операций предложена методика формовки и отливки в одной опоке двух каркасов на двух моделях (рис. 63). По этой методике технологический процесс состоит в следующем. Из алюминия изготавливают поддон квадратной формы с литниковой чашей посередине и разрезом посередине. Обе половины поддона покрывают воском. Устанавливают и закрепляют огнеупорные модели с отмоделированными восковыми каркасами на каж-
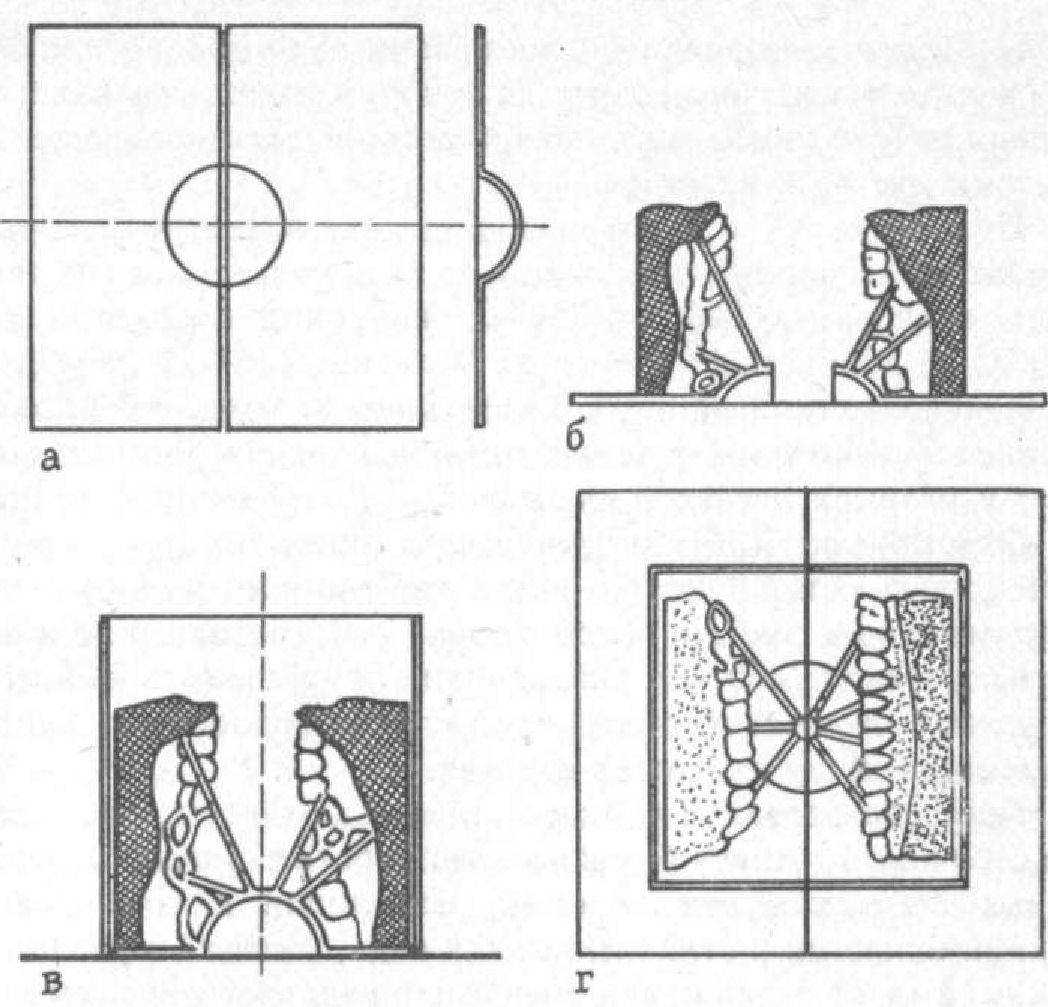
63. Схема формовки (С. Д. Богословский):.
а — разрезанный поддон, б—установка огнеупорных моделей с лнтннквми, а, г сборка двух моделей нэ огнеупорного материала в квадратной опоке.
дой половине поддона и покрывают восковые репродукции огнеупорной массой. Соединяют половины поддона, склеивают их воском и устанавливают в квадратную опоку с последующим заполнением формовочной массой.
Дальнейшие этапы изготовления каркаса бюгельного протеза не отличаются от описанных выше.
Выплавление восковой модели и прокаливание литейной формы производят в следующем порядке. Снимают подставку после ее предварительного подогревания во избежание повреждения восковой формы и облицовочного слоя, устанавливают кювету-опоку на поддон воронкой вниз для стекания воска и переносят в печь, нагретую до 200 "С на 20—25 мин для окончательного удаления воска. Устанавливают опоку в прокалочную печь с температурой 400 °С, доводят ее до 800 900 °С в течение I `/г ч, выдерживают при этой температуре 20—30 мин и переносят в печь для заливки металлом.
Хорошее прокаливание литейной формы обеспечивает хоэошие литейные свойства металлу, уменьшает его усадку, (Сключает газовыделение при заливке металла.
Пользоваться прокалочными печами для выплавления воска нельзя, так как возникающая при этом копоть увеличивает содержание углерода в отливке и, засоряя электронагреватели, выводит печь из строя.
При литье на огнеупорных моделях, в состав которых входит кристобаллит, незначительно расширяющийся в интервале температур 220 °С4260 °С, подъем температуры от 200
С до 300
С надо проводить медленно (30—40 мин) для удаления кристаллизационной воды и газов. Ускоренное повышение температуры в этом интервале приводит к растрескиванию и разрыву литейной формы.
Очистку литья от керамического покрытия производят с помощью металлических щеток или химическим способом с применением гидрата окиси калия, расплавленного до жидкого состояния (360 °С). Опущенная в эту жидкость на 2 мин отливка полностью освобождается от огнеупорного материала и готова для последующей отделки.
При использовании химического метода очистки необходимо соблюдать технику безопасности: работать в очках и резиновых перчатках при хорошей вентиляции и совершенно сухими щипцами и отливке, так как вода, попадая в расплавленный гидрат окиси калия, мгновенно испаряется, что может привести к выбрасыванию жидкости из ковша.
Очистка литья может быть произведена и в корундоструй ном аппарате с использованием корундового абразива с вели чиной зерен 1 мм. Присоединенные пылесос и компрессор создают необходимые условия для очистки литья от огнеупорной массы.
После отделения литников с помощью вулканитовых дисков каркас подвергают механической обработке, шлифовке н полировке.
Механическую обработку каркаса бюгельного протеза из КХС производят абразивными кругами и фасонными головками повышенной твердости. При этом, зачищая заусеницы и наплывы на отливке, необходимо следить за сохранением толщины и рельефа поверхности, прилегающей к зубам и слизистой оболочке.
Для сглаживания поверхности отливки и подготовки ее к полировке производят шлифовку резиновыми элэстичными кругами, изготовленными из абразивов на вулканнтовой основе. Движения надо производить плавно, без сильного давления.
Последним этапом изготовления каркаса бюгельного протеза является полировка, которая должна быть произведена до постановки зубов и формовки базиса пластмассой.
Полировку производят с помощью мягких нитяных щеток н полировочных паст, добиваясь зеркального блеска для обеспечения его гигиеничности, прочности и предупреждения повреждений тканей зуба кламмерами Полируют все поверхности, кроме сетки седловидной части.
Полировку каркаса бюгельного протеза из сплава КХС можно произвести электролитическим способом. Для этого в фарфоровый сосуд вместимостью 120 мл, высотой 150 мм помещают катод (пластина нержавеющей стали размером 76 X 38 X О-
): анодом служит каркас протеза. В сосуд наливают электролит (1 —1,5 л), в состав которого входят этиловый спирт (120 г), вода дистиллированная (120 г), кислота ортофосфорная (120 г), этиленгликоль (540 г), кислота серная концентрированная (120 г) (при приготовлении раствора серную кислоту приливают к этиленгликолю).
В качестве источника тока служит выпрямитель силовой ВС-24, дающий ток силон до 6 А напряжением до 24 В.
После шлифовки каркас бюгельного протеза укрепляют в сосуде на расстоянии 40 мм от катода и в процессе его нахождения в электролите регулярно поворачивают. Режим полировки: сила тока — 2 А, время — 10—15 мин с последующей промывкой в воде.
Дальнейшие этапы изготовления бюгельного протеза включают формирование воскового базиса и постановку искусственных зубов с последующей гипсовкой в кювету и заменой воска пластмассой,.
Гипсовку модели в кювету производят обратным способом с переводом всего каркаса и искусственных зубов в противоположную часть кюветы.